- My Forums
- Tiger Rant
- LSU Recruiting
- SEC Rant
- Saints Talk
- Pelicans Talk
- More Sports Board
- Fantasy Sports
- Golf Board
- Soccer Board
- O-T Lounge
- Tech Board
- Home/Garden Board
- Outdoor Board
- Health/Fitness Board
- Movie/TV Board
- Book Board
- Music Board
- Political Talk
- Money Talk
- Fark Board
- Gaming Board
- Travel Board
- Food/Drink Board
- Ticket Exchange
- TD Help Board
Customize My Forums- View All Forums
- Show Left Links
- Topic Sort Options
- Trending Topics
- Recent Topics
- Active Topics
Started By
Message
Welders, need assistance on grounding
Posted on 11/19/19 at 1:34 pm
Posted on 11/19/19 at 1:34 pm
I want to make some Christmas trees for the yard to string lights to out of rebar. I'm new to welding. I have a flux core welder. Can I clamp the ground to one of the pieces of rebar I'm welding, or do I have to have a welding table?
Posted on 11/19/19 at 1:36 pm to VanRIch
not real sure what your question here about a welding table is but you connect the ground lead to whatever metal you're welding
Posted on 11/19/19 at 1:37 pm to Bedhog
I didn't know if I needed a metal table to ground and then have both pieces of material on that or would it be sufficient to just ground to one piece of material.
Posted on 11/19/19 at 1:40 pm to VanRIch
the metal weld table simply allows current to run thru it to the piece you're welding. It's best to ground directly to the piece you are welding.
Posted on 11/19/19 at 1:49 pm to Bedhog
Ok, good deal. So I can support two pieces of rebar on saw horses (that won't be near the actual welding) but up two pieces of rebar so they're touching, clamp the ground to either one of them, then weld? Doesn't need to be pretty, just a solid weld. I'll be buying a cheap angle grinder from harbor freight with a wire wheel to clean up the rebar first.
Posted on 11/19/19 at 1:56 pm to VanRIch
No offense intended but if you have to ask this question then the rest is worth bringing up, what does the rest of your setup look like?
Even though the welder has a normal 110V plug on it, it's going to draw a shite load of amps to even put a puny weld on rebar. Ideally you need to be on a 20 amp dedicated circuit, and if that's not an option you need to take steps to turn off anything else drawing power on that circuit while the welder is running. It's still not a great idea.
I'm not a pro by any means but I've significantly decreased the shittiness of my flux core welds by using a mapp gas torch to preheat the area before welding and grinding all bonding surfaces down to clean metal before.
Even though the welder has a normal 110V plug on it, it's going to draw a shite load of amps to even put a puny weld on rebar. Ideally you need to be on a 20 amp dedicated circuit, and if that's not an option you need to take steps to turn off anything else drawing power on that circuit while the welder is running. It's still not a great idea.
I'm not a pro by any means but I've significantly decreased the shittiness of my flux core welds by using a mapp gas torch to preheat the area before welding and grinding all bonding surfaces down to clean metal before.
Posted on 11/19/19 at 2:06 pm to TheDrunkenTigah
None taken. I do have a dedicated circuit for my Christmas lights, but not sure what amp it is. It is 2 pole and then connects to a timer box. Not sure if I can use that, I'd have to get a heavy duty extension cord as all the outlets to this circuit are in my eaves.
Posted on 11/19/19 at 2:25 pm to VanRIch
I would highly suggest moving this operation to the garage or renting/borrowing a generator. Very good chance you'll burn up the timer box, or worse.
A 20 amp plug will look like this:
You can verify by looking in the breaker box if you know the circuit the outlet is on. Bare minimum you will need a 15 amp outlet and breaker, which is much more common. You want to be as close to the breaker panel as possible. On a 15 amp circuit you will likely trip the breaker a lot unless you weld in short bursts, or something is going to melt. Extension cords are a no-no unless they cost more than the welder likely did.
Flux core welders are meant to weld very thin material, and rebar is by no definition thin. It still can be done but you will need to take steps to help yourself. You're on the right track with the grinder but I would also clamp the two pieces of rebar together, and maybe notch them a bit so they fit together pretty snug. Welding two round objects together is going to be a pain in the arse. Grind clean the area where your ground clamp is so it will make good contact. Heat the ever living shite out the rebar with a torch and your welds will stick much better. Be prepared to go slow and work in 5 minute intervals, which is likely the duty cycle of your welder at max amps.
Not trying to discourage you, but I recently learned all of this the hard way myself. There's a good reason that a proper welding setup costs thousands of dollars, but as long as you don't expect it to be pretty you can get by.
A 20 amp plug will look like this:
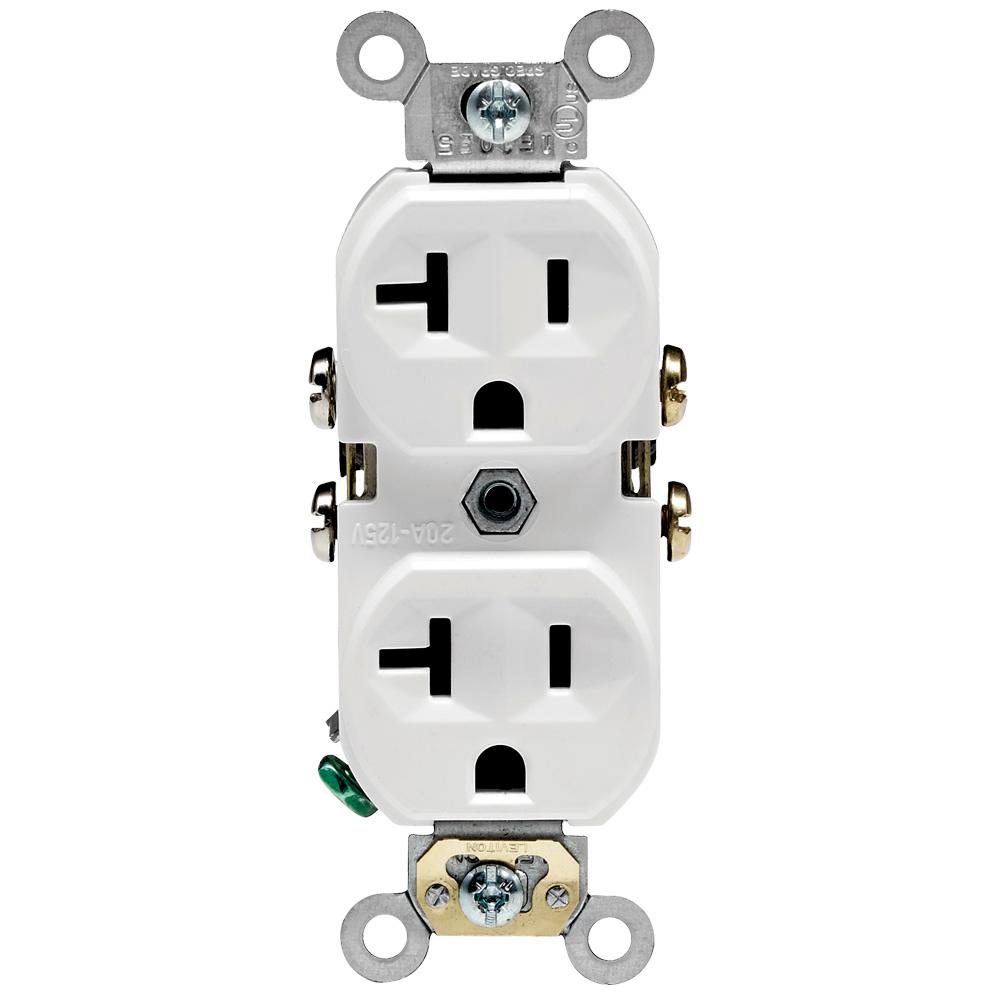
You can verify by looking in the breaker box if you know the circuit the outlet is on. Bare minimum you will need a 15 amp outlet and breaker, which is much more common. You want to be as close to the breaker panel as possible. On a 15 amp circuit you will likely trip the breaker a lot unless you weld in short bursts, or something is going to melt. Extension cords are a no-no unless they cost more than the welder likely did.
Flux core welders are meant to weld very thin material, and rebar is by no definition thin. It still can be done but you will need to take steps to help yourself. You're on the right track with the grinder but I would also clamp the two pieces of rebar together, and maybe notch them a bit so they fit together pretty snug. Welding two round objects together is going to be a pain in the arse. Grind clean the area where your ground clamp is so it will make good contact. Heat the ever living shite out the rebar with a torch and your welds will stick much better. Be prepared to go slow and work in 5 minute intervals, which is likely the duty cycle of your welder at max amps.
Not trying to discourage you, but I recently learned all of this the hard way myself. There's a good reason that a proper welding setup costs thousands of dollars, but as long as you don't expect it to be pretty you can get by.
Posted on 11/19/19 at 2:46 pm to TheDrunkenTigah
I thought they were preferable for thicker materials. That's what I'm reading anyway. I had thought about overlapping the rebar and then welding some flat stock to both sides. Not sure if that makes sense.
Posted on 11/19/19 at 3:23 pm to VanRIch
In general, the thicker the metal the more amps you need. A flux core running on regular outlet power will be doing good to get 80 amps, where a professional would probably use 150-200 amps to weld rebar.
Thick metal wicks away the heat you need to actually melt what you're welding and get it to fuse together. That's where the torch comes in. If you can get it nice and hot before you start welding then the welder doesn't have to do the work of heating it. Propane is better than nothing but the mapp gas will be right next to it on the shelf at home depot and burns much hotter.
Thick metal wicks away the heat you need to actually melt what you're welding and get it to fuse together. That's where the torch comes in. If you can get it nice and hot before you start welding then the welder doesn't have to do the work of heating it. Propane is better than nothing but the mapp gas will be right next to it on the shelf at home depot and burns much hotter.
Posted on 11/19/19 at 3:38 pm to TheDrunkenTigah
quote:
No offense intended but if you have to ask this question then the rest is worth bringing up, what does the rest of your setup look like?
I would modify your statement to say, "if you have to ask this question, then you have no business turning on a welder."
To the OP, you are getting a lot of advice without anyone even bothering to ask what welder you have, how many amps it draws, its power rating and duty cycle. The duty cycle probably doesn't matter much, or shouldn't for the types of welds you are describing, but you need to know the answer the to the question you are asking, and probably many more that you should ask, before you start this project.
Posted on 11/19/19 at 3:54 pm to BiggerBear
quote:
I would modify your statement to say, "if you have to ask this question, then you have no business turning on a welder."
I can't stand arrogant statements like this. No one is born knowing anything, we all have to learn everything at some point. This is a message board where many people ask for help on all sorts of things. I don't ever give anyone shite for asking questions about things they're trying to learn.
Posted on 11/19/19 at 4:30 pm to BiggerBear
quote:
To the OP, you are getting a lot of advice without anyone even bothering to ask what welder you have, how many amps it draws, its power rating and duty cycle.
He stated it’s a flux core machine, and almost across the board they have roughly the same specs on the entry level models. All that differs between them is the quality of the wire feed and nick nacks in the box. Without looking at it I can tell you it will put out about 80 amps at 18V with a 20% duty cycle drawing 20 amps out of the wall. He will have the amp dial all the way up to get any penetration in rebar, which is why I started off telling him to get the power source squared away first. All the box stores have been selling these entry level flux core machines for a couple years now, so not that hard to figure out what OP is working with. Nothing wrong with the guy asking questions.
This post was edited on 11/19/19 at 4:44 pm
Posted on 11/19/19 at 7:59 pm to VanRIch
You can easily tack up rebar with even a small flux-core machine. I have a multi-process unit and dedicated 220V/50A outlets in my garage and shop but it's a 120/240 machine and I've tested it on 120V and with .035 Lincoln wire it could handle what you are doing easily. It's not technically a ground clamp, since polarity doesn't always mean the clamp is the ground connection here and many will call it a material clamp or work piece clamp. You'll just want to put the clamp on a good clean spot as close as you can to were you are welding to give your little machine the best chance. Pre-heating the weld area with a torch will help a lot. Another thing is fixturing the pieces you are welding, you can never have enough clamps, magnets, and square surfaces to keep your work tied together when welding.
I think I'm going to make a re-bar tree myself now...
I think I'm going to make a re-bar tree myself now...

Posted on 11/19/19 at 8:48 pm to Clames
Posted on 11/21/19 at 4:07 pm to VanRIch
quote:
I can't stand arrogant statements like this. No one is born knowing anything, we all have to learn everything at some point.
And learning how to properly ground a welder is something that should be learned before you turn it on. It wasn't arrogance - it was a warning. I'd tell you not to be a dumbass but it looks like its too late.
Posted on 11/21/19 at 9:41 pm to BiggerBear
The work lead is not grounding the metal anyway. It’s simply completing the circuit to either the positive polarity stud on the machine. You can clamp it to the workpiece or the metal table - doesn’t really matter as long as there’s a good conductive path. The machine frame is grounded through it’s own plug.
I would clean the rebar with a hard rock or flap disk to give yourself the best advantage you can. Watch a few welding tips and tricks YouTube videos and let it rip.
I would clean the rebar with a hard rock or flap disk to give yourself the best advantage you can. Watch a few welding tips and tricks YouTube videos and let it rip.
This post was edited on 11/21/19 at 9:45 pm
Popular
Back to top
