- My Forums
- Tiger Rant
- LSU Recruiting
- SEC Rant
- Saints Talk
- Pelicans Talk
- More Sports Board
- Fantasy Sports
- Golf Board
- Soccer Board
- O-T Lounge
- Tech Board
- Home/Garden Board
- Outdoor Board
- Health/Fitness Board
- Movie/TV Board
- Book Board
- Music Board
- Political Talk
- Money Talk
- Fark Board
- Gaming Board
- Travel Board
- Food/Drink Board
- Ticket Exchange
- TD Help Board
Customize My Forums- View All Forums
- Show Left Links
- Topic Sort Options
- Trending Topics
- Recent Topics
- Active Topics
Started By
Message
Finishing an 80% AR 15 lower receiver with the Easy Jig mini review
Posted on 6/9/15 at 8:18 am
Posted on 6/9/15 at 8:18 am
I wanted to build my own AR15 from scratch. After months of reading and research on the AR platform I decided to also do an 80% lower as well. I eventual decided after months of back and forth that I using one of the router base jigs looked to be the easiest way to finish an aluminum lower.
Finished my first 80% lower with my 80% arms Easy Jig. I had read everything there was to read and watched every available video about using the Easy Jig that was available on the internet and I was pretty confident I knew exactly what to expect. Even with all of the book learning nothing beats good old fashioned experience in doing something to really learn how to do it. I got my easy jig, the 80% arms 3/4" length of cut 1/4" end mill, my set of drill bits out of my tool box, and a 3 pack of Tactical Machining forged 7075 80% lowers. I highly recommend getting the 80% arms end mill. I looked everywhere for a cheaper alternative, and it's not worth trying to save $4-5. Their end mill works well and you don't have to worry about milling into your jig. Get it, it's worth it.
Starting off with the drilling which should have been the most straight forward and easy part of the process. My handy chart said to use a drill speed of between 2k-3kRPM for aluminum with a 3/8" drill bit. I originally went with 2180 RPM setting on my old Delta 8" benchtop drill press. It's a good 15 years old but looks almost exactly like the current el cheapo 8" benchtop drill press from harbor freight. With a jobbers length 3/8" bit (~5" long) I could not fit the jig on the table and slide it under the bit. Moving the table out of the way my drill press didn't have enough throw to drill the holes deep enough. To get around this I had to move the table out of the way, pick the jig up sliding the drill bit into the hole I want to drill, and slide the table back under the jig. Didn't take too long to realize my little drill press didn't quite have the omph even at 2180 RPM the drill press was noticeably bogging down even with proper lubrication and pecking. I dropped the RPMs to 1630 which slowed my drilling down a bit and the drill press performed much better at those speeds. Good machining practice keeping the chips clear and keeping the drill bit lubed and checking my drill stop collar frequently for slippage found all of the holes drilled in less than 30 minutes and that was taking it slow.
Next came the milling. I had a Blue Hawk (Lowes Brand) el cheapo plunge router that I had bought for $79 *with a router table* for another project. $79 with a router table? Yeah it's a cheap PoS :D It looks a lot like the Black and Decker RP250 that 80% arms does not recommend. I'm sure they came out of the same Chinese factory rebadged for Lowes. I figured I would give it a shot and see if it would work. If not I would invest in another router.
Don't the look suspiciously alike?
I made a couple of mistakes in the beginning but after about half way through my first lower I found my groove and got into a rhythm. In no particular order, my main mistakes were:
1. [span style='font-weight: bold;']Trying to remove too much material.[/span] In my excitement of wanting to get this done the first couple of passes I tried to remove "1/3" of the hash mark. I was getting a lot of chatter with that depth of cut. I tried adjusting the router speed up and down but was still getting chatter. 80% arms says to do 1/4 to 1/5 a hash mark per pass. This leads me directly to item number 2.
2. [span style='font-weight: bold;']Not using the depth adjustment/measurement tools on my router for a more consistent depth change from pass to pass.[/span] Trying to use the included cutting gauge that is built into the jig was pretty difficult when using a plunge router. Trying to hold the gauge pushing down on the plunger to get the depth set consistently... well that was a very inconsistent operation. After a couple of passes I finally wised up, abandoned the depth gauge build into the jig to adjust my cutting depth using it only for periodic sanity checks and started using the depth controls built into my router. I found I could get a really smooth cut when I cut at a depth of 3/64" or less. I found I could actually cut faster using the shallower cut because I didn't have to be as slow or steady when making the pass.
Walls get smoother as I go down the lower.
3. [span style='font-weight: bold;']Not cleaning my collet or tightening my collet tight enough.[/span] My router has been used on wood projects and has bits of wood dust all over it. I should have cleaned the collet out before I started but I just jammed the end mill (backed it off about 1/4") and started milling. About half way through my 2nd pass the router was really starting to jump a lot. I futzed with the speed (RPMs and the speed I was moving the router) but it was only getting worse and worse. After I finished that pass that's when I noticed my bit had backed out almost 1/4". Then I vacuumed the collet out, blew compressed air in there, and swabbed it with some alcohol soaked Q-tips to pick up all of the fine wood dust. I tightened the crap out of it and didn't have any issues after that.
After bottoming my router on the jig's depth guide I thought I was done. Well it turns out I wasn't.
Jig is bottom out! I'm done!
Wait... it looks like I'm a 32nd out from the 1.249" number. That's not within the 1.249" +/- 0.01" tolerance.
Breaking out the calipers verifies that I'm still outside of tolerance.
I took two more really light ~1/64" passes to sneak up on 1.249"
Finished my first 80% lower with my 80% arms Easy Jig. I had read everything there was to read and watched every available video about using the Easy Jig that was available on the internet and I was pretty confident I knew exactly what to expect. Even with all of the book learning nothing beats good old fashioned experience in doing something to really learn how to do it. I got my easy jig, the 80% arms 3/4" length of cut 1/4" end mill, my set of drill bits out of my tool box, and a 3 pack of Tactical Machining forged 7075 80% lowers. I highly recommend getting the 80% arms end mill. I looked everywhere for a cheaper alternative, and it's not worth trying to save $4-5. Their end mill works well and you don't have to worry about milling into your jig. Get it, it's worth it.
Starting off with the drilling which should have been the most straight forward and easy part of the process. My handy chart said to use a drill speed of between 2k-3kRPM for aluminum with a 3/8" drill bit. I originally went with 2180 RPM setting on my old Delta 8" benchtop drill press. It's a good 15 years old but looks almost exactly like the current el cheapo 8" benchtop drill press from harbor freight. With a jobbers length 3/8" bit (~5" long) I could not fit the jig on the table and slide it under the bit. Moving the table out of the way my drill press didn't have enough throw to drill the holes deep enough. To get around this I had to move the table out of the way, pick the jig up sliding the drill bit into the hole I want to drill, and slide the table back under the jig. Didn't take too long to realize my little drill press didn't quite have the omph even at 2180 RPM the drill press was noticeably bogging down even with proper lubrication and pecking. I dropped the RPMs to 1630 which slowed my drilling down a bit and the drill press performed much better at those speeds. Good machining practice keeping the chips clear and keeping the drill bit lubed and checking my drill stop collar frequently for slippage found all of the holes drilled in less than 30 minutes and that was taking it slow.
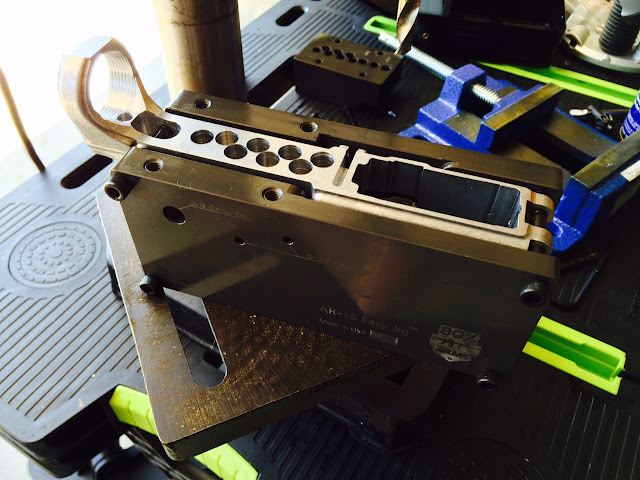
Next came the milling. I had a Blue Hawk (Lowes Brand) el cheapo plunge router that I had bought for $79 *with a router table* for another project. $79 with a router table? Yeah it's a cheap PoS :D It looks a lot like the Black and Decker RP250 that 80% arms does not recommend. I'm sure they came out of the same Chinese factory rebadged for Lowes. I figured I would give it a shot and see if it would work. If not I would invest in another router.
Don't the look suspiciously alike?
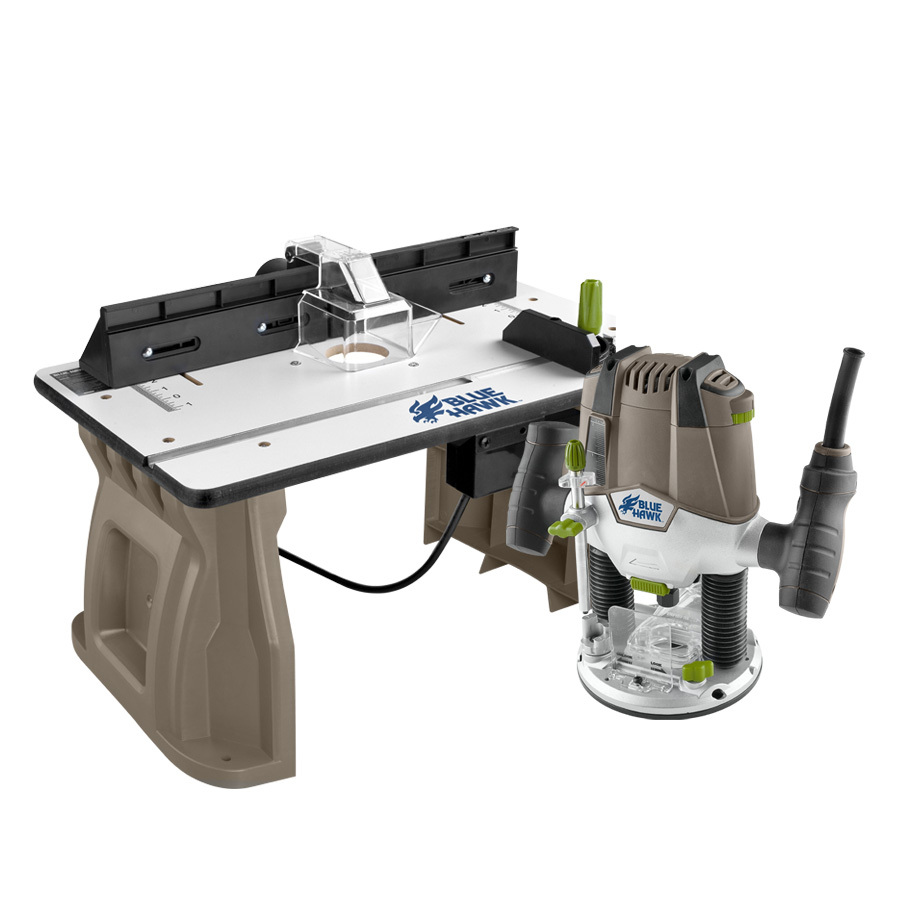

I made a couple of mistakes in the beginning but after about half way through my first lower I found my groove and got into a rhythm. In no particular order, my main mistakes were:
1. [span style='font-weight: bold;']Trying to remove too much material.[/span] In my excitement of wanting to get this done the first couple of passes I tried to remove "1/3" of the hash mark. I was getting a lot of chatter with that depth of cut. I tried adjusting the router speed up and down but was still getting chatter. 80% arms says to do 1/4 to 1/5 a hash mark per pass. This leads me directly to item number 2.
2. [span style='font-weight: bold;']Not using the depth adjustment/measurement tools on my router for a more consistent depth change from pass to pass.[/span] Trying to use the included cutting gauge that is built into the jig was pretty difficult when using a plunge router. Trying to hold the gauge pushing down on the plunger to get the depth set consistently... well that was a very inconsistent operation. After a couple of passes I finally wised up, abandoned the depth gauge build into the jig to adjust my cutting depth using it only for periodic sanity checks and started using the depth controls built into my router. I found I could get a really smooth cut when I cut at a depth of 3/64" or less. I found I could actually cut faster using the shallower cut because I didn't have to be as slow or steady when making the pass.
Walls get smoother as I go down the lower.
3. [span style='font-weight: bold;']Not cleaning my collet or tightening my collet tight enough.[/span] My router has been used on wood projects and has bits of wood dust all over it. I should have cleaned the collet out before I started but I just jammed the end mill (backed it off about 1/4") and started milling. About half way through my 2nd pass the router was really starting to jump a lot. I futzed with the speed (RPMs and the speed I was moving the router) but it was only getting worse and worse. After I finished that pass that's when I noticed my bit had backed out almost 1/4". Then I vacuumed the collet out, blew compressed air in there, and swabbed it with some alcohol soaked Q-tips to pick up all of the fine wood dust. I tightened the crap out of it and didn't have any issues after that.
After bottoming my router on the jig's depth guide I thought I was done. Well it turns out I wasn't.
Jig is bottom out! I'm done!

Wait... it looks like I'm a 32nd out from the 1.249" number. That's not within the 1.249" +/- 0.01" tolerance.

Breaking out the calipers verifies that I'm still outside of tolerance.

I took two more really light ~1/64" passes to sneak up on 1.249"
Posted on 6/9/15 at 8:18 am to DeoreDX
Since my lower came with the rear take take down area already milled I didn't bother removing the material between the fire control pocket and the rear take down shelf.
After reading a lot of horror stories on milling out the trigger hole I read over on another site several people having success milling the trigger hole using a different method than the one listed in the instructions for the easy jig. User JAE on the site suggested not drilling the hole for the trigger slot. Instead he bottomed the mill out on the bottom of the lower. Then lowered the end mill just a hair, I did it in 1/64" steps. Then you rest one edge of the router on the work surface and tilt the router down to begin your cutting pass. After tilting the router down your make your pass. It took me 5 passes this way and I ended up with a very clean trigger pocket. I haven't tried it any other way but this way was very easy and made a very nice clean trigger pocket.
After finishing the trigger slot I was home free. Couple of hits with the drill press and I had a completed lower. I've learned a lot doing my first lower. I expect my next two to be much improved over this first one. It's been a 5 month journey since I started researching my first AR and this lower was past piece of the puzzle and is now complete. I'm glad I spent a little extra on the Easy jig over drill press jigs or settling for a polymer 80% lower. I have zero regrets with my choice of the Easy jig and would choose it again for my 80% build if I had to do it over again. Only way I could improve it I think is if I spent way more money on a mini mill.
Built up my lower (picture is sans rear takedown pin because I dropped my detent and they make detents out of material that evaporates on contact with the ground) and happy to say everything checks out functionally. Maiden voyage saw 120 rounds down range without a single hiccup. Rifle cycled correctly and bolt hold open functioned correctly. It's been a fun journey and I've learned a lot. Big thanks to ARFCOM and calguns.net which has been an invaluable resource on the AR platform and 80% builds my first build. I'm proud to say I installed every pin, spring, and nut on this rifle.

After reading a lot of horror stories on milling out the trigger hole I read over on another site several people having success milling the trigger hole using a different method than the one listed in the instructions for the easy jig. User JAE on the site suggested not drilling the hole for the trigger slot. Instead he bottomed the mill out on the bottom of the lower. Then lowered the end mill just a hair, I did it in 1/64" steps. Then you rest one edge of the router on the work surface and tilt the router down to begin your cutting pass. After tilting the router down your make your pass. It took me 5 passes this way and I ended up with a very clean trigger pocket. I haven't tried it any other way but this way was very easy and made a very nice clean trigger pocket.
After finishing the trigger slot I was home free. Couple of hits with the drill press and I had a completed lower. I've learned a lot doing my first lower. I expect my next two to be much improved over this first one. It's been a 5 month journey since I started researching my first AR and this lower was past piece of the puzzle and is now complete. I'm glad I spent a little extra on the Easy jig over drill press jigs or settling for a polymer 80% lower. I have zero regrets with my choice of the Easy jig and would choose it again for my 80% build if I had to do it over again. Only way I could improve it I think is if I spent way more money on a mini mill.
Built up my lower (picture is sans rear takedown pin because I dropped my detent and they make detents out of material that evaporates on contact with the ground) and happy to say everything checks out functionally. Maiden voyage saw 120 rounds down range without a single hiccup. Rifle cycled correctly and bolt hold open functioned correctly. It's been a fun journey and I've learned a lot. Big thanks to ARFCOM and calguns.net which has been an invaluable resource on the AR platform and 80% builds my first build. I'm proud to say I installed every pin, spring, and nut on this rifle.
This post was edited on 6/9/15 at 8:19 am
Posted on 6/9/15 at 8:24 am to DeoreDX
I did a second lower last week. This one was a 6061 lower from 80% arms. 6061 was way easier to machine than the 7075. This one did NOT have the rear takedown shelf milled. Chalk this up as another lesson learned but if you are having to mill the rear shelf make sure the hole you drill for the rear shelf that passes through the rear jig retainer bolt is drilled with a brand new (or at least really sharp) drill bit. Of not you will have to exert enough pressure to drill that you rotate the lower in the jig.
BTW... 80% lowers are like potato chips, you can never have only one! This one is going on the rifle upper I had previously made.
BTW... 80% lowers are like potato chips, you can never have only one! This one is going on the rifle upper I had previously made.
Posted on 6/9/15 at 10:05 am to DeoreDX
Very nice. I've looked at the easy jig also, but haven't pulled the trigger yet. I don't have a drill press, but they say it isn't necessary. I do have a standard drill and access to a router, but I'm concerned I don't have the experience to complete a project of this magnitude.
Posted on 6/9/15 at 10:08 am to SquirrelBones
I have a drill press. I may end up trying this.
Posted on 6/9/15 at 10:31 am to SquirrelBones
quote:
I do have a standard drill and access to a router, but I'm concerned I don't have the experience to complete a project of this magnitude.
I don't think you need a drill press. Just take it slow when machining and it really is pretty easy. When I say take it slow I mean try not to remove too much material at a time. Shallow passes make for easy passes. Also if you are worried about it the 6061 billet receiver from 80% arms is much easier to do than the 7075. 80% arms will send you a free receiver of your choice of you buy an easy jig and post a review with pictures on the Internet. That is how I got my 6061 lower.
https://www.80percentarms.com/pages/free-lower-promotion

Posted on 6/9/15 at 10:34 am to Broke
quote:You should see his golf threads.
This is how a thread is done
Posted on 6/9/15 at 10:36 am to AlxTgr
quote:
You should see his golf threads.
Yeah but I don't care about golf.
Posted on 6/9/15 at 10:45 am to Broke
I don't care that you don't care.
Posted on 6/9/15 at 12:44 pm to DeoreDX
Awesome post. Thanks for sharing this. 

Posted on 6/9/15 at 1:58 pm to DeoreDX
That's impressive. I don't understand it all, but I'm impressed.
Posted on 6/9/15 at 4:41 pm to DeoreDX
I purchased a 7075 lower from 80% Arms but I don't have a drill press and have been hesitant to do it without one.
Couple questions for you:
1. If I have a bench-mounted vise, could this be feasible to drill out using a handheld battery drill? Or would it just be much more difficult?
2. Did milling through the anodizing cause any cracks to form? I bought an anodized lower and was told by a friend I made a mistake. But it's nice to see that on your second lower you went straight through with no issues.
3. If I don't have a router, what is another method I could use to get the inside entirely milled after drilling everything?
4. Are you close to the Baton Rouge area so I can use your drill press?
Thanks in advance.
Couple questions for you:
1. If I have a bench-mounted vise, could this be feasible to drill out using a handheld battery drill? Or would it just be much more difficult?
2. Did milling through the anodizing cause any cracks to form? I bought an anodized lower and was told by a friend I made a mistake. But it's nice to see that on your second lower you went straight through with no issues.
3. If I don't have a router, what is another method I could use to get the inside entirely milled after drilling everything?
4. Are you close to the Baton Rouge area so I can use your drill press?

Thanks in advance.

Posted on 6/9/15 at 4:48 pm to bapple
quote:
Are you close to the Baton Rouge area so I can use your drill press?
Want to do this co-op? I have one. We can frick your lower up first and then do mine.
Posted on 6/9/15 at 7:22 pm to Broke
quote:
Want to do this co-op? I have one. We can frick your lower up first and then do mine.
In.
Email me. Bigapple828@aim.com
Posted on 6/9/15 at 7:54 pm to Broke
quote:
I have one. We can frick your lower up first and then do mine.


Posted on 6/9/15 at 7:59 pm to bapple
Hit me up when yall f shite up.
Posted on 6/12/15 at 4:06 pm to Ice Cream Sammich

Popular
Back to top
